Bentonit Kil Sondaj Çamuru: The Ultimate Guide to Enhanced Drilling Performance
Bentonite clay stands as a fundamental component in modern drilling operations, revolutionizing the efficiency and safety of drilling processes across industries. This naturally occurring clay, primarily composed of montmorillonite minerals, has become indispensable in drilling applications due to its exceptional properties and versatility.
When incorporated into drilling fluids, bentonite clay transforms ordinary water into a powerful drilling mud that addresses multiple critical challenges simultaneously. From maintaining borehole stability to efficiently removing cuttings, bentonite drilling mud serves as the backbone of successful drilling operations worldwide.
This comprehensive guide explores everything you need to know about bentonite clay drilling mud – from its composition and properties to application techniques and troubleshooting. Whether you’re a drilling professional seeking to optimize your operations or someone looking to understand the science behind effective drilling practices, this resource provides valuable insights into maximizing the benefits of bentonite clay in drilling applications.
Bentonit Kili Nedir?? Understanding the Foundation of Drilling Mud Composition and Origin
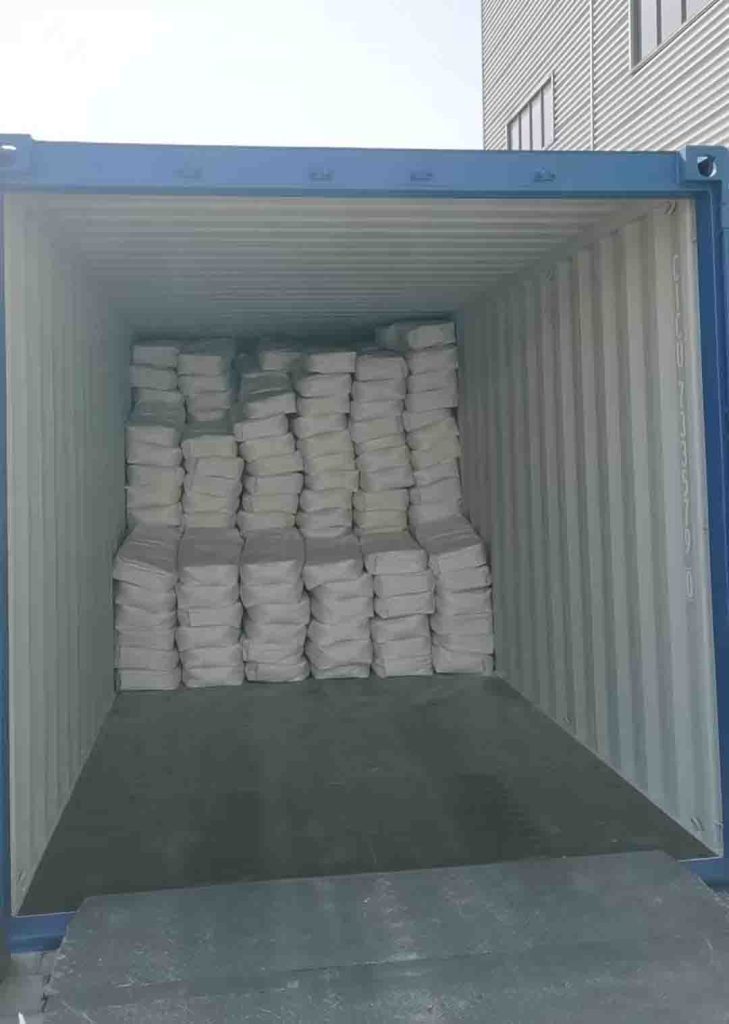
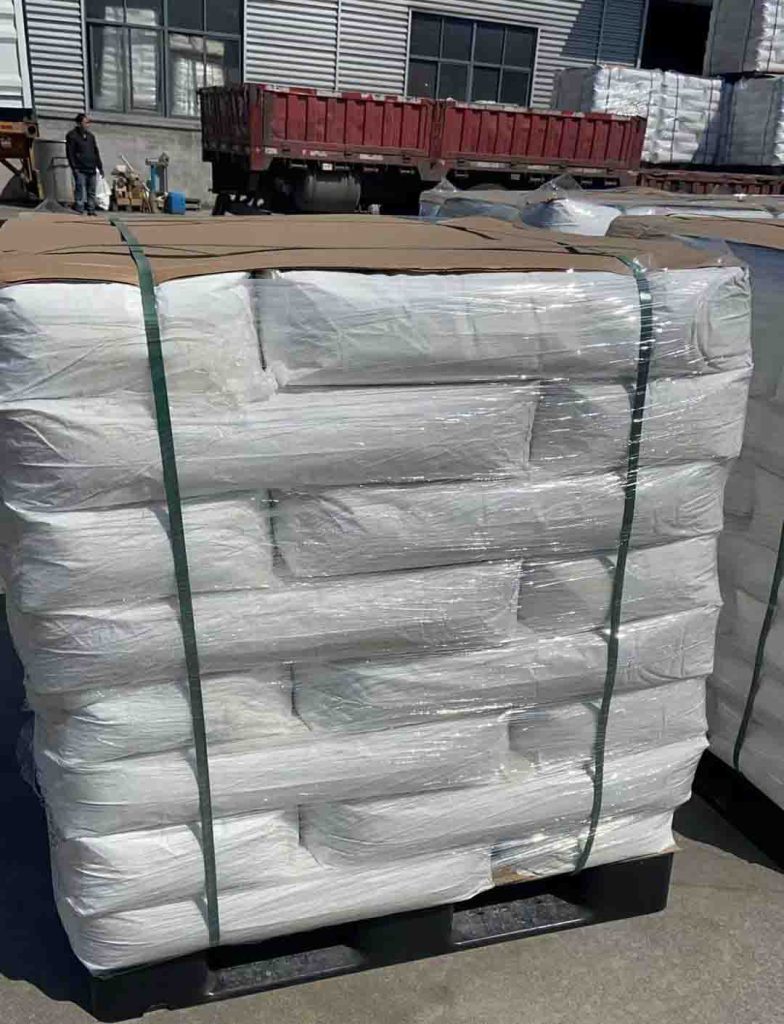
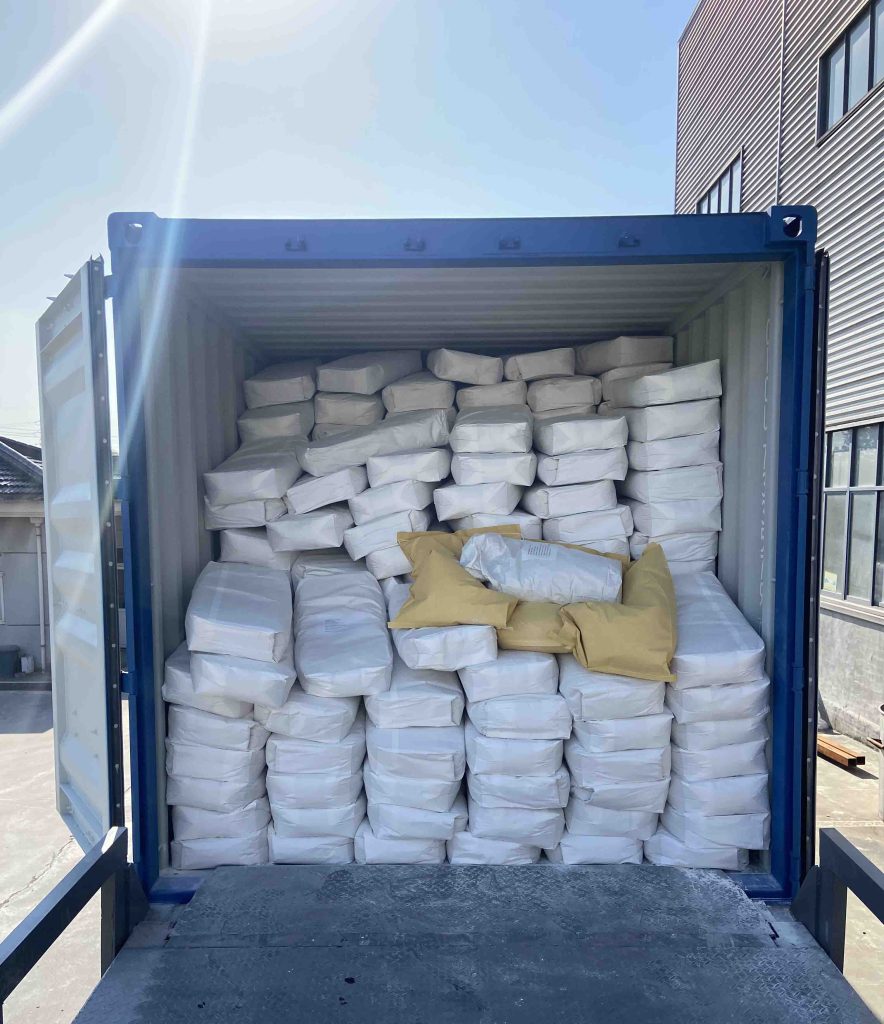
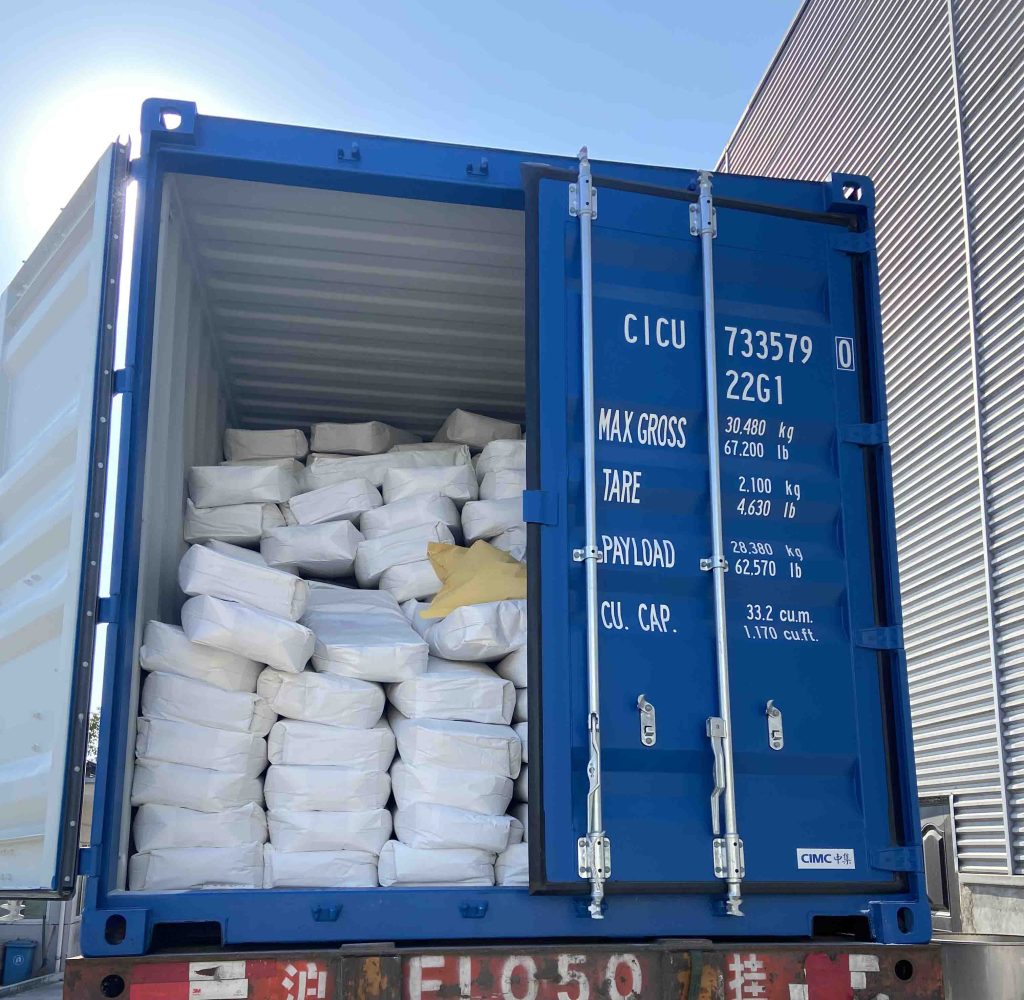
Bentonite is a naturally occurring clay mineral formed from the weathering of volcanic ash in the presence of water. Named after Fort Benton, Wyoming, where significant deposits were first discovered, this remarkable material consists primarily of montmorillonite (60-80%), a member of the smectite group of clay minerals.
The geological formation of bentonite occurs when volcanic ash settles in marine
environments and undergoes alteration over time. This unique origin contributes to bentonite’s exceptional properties, particularly its ability to absorb and retain water. The inner surface area of just one gram of bentonite ranges from 400 ile 600 square meters –dramatically higher than ordinary clay, which typically has only about 2 square meters.
Types of Bentonite Clay
Not all bentonite clay drilling mud are created equal. The two primary classifications include:
- Sodyum Bentonit: Characterized by its exceptional swelling capacity, sodium
bentonite can expand up to 15-18 times its dry volume when hydrated. This variety
is preferred for drilling applications due to its superior viscosity and gel-forming
özellikler. Wyoming bentonite is renowned as one of the highest quality sodium
bentonites available.
- Calcium Bentonite: With more limited swelling capacity (typically 2-3 times its dry
volume), calcium bentonite finds applications in other industries but is less
suitable for drilling operations unless treated with additives like sodium carbonate
to enhance its properties.
For drilling mud applications, high-quality sodium bentonite is the industry standard,
with API (American Petroleum Institute) specifications providing benchmarks for
performance and quality.
The Science Behind Bentonite’s Effectiveness in Drilling
Thixotropic Behavior: The Key to Performance
One of bentonite’s most valuable properties in drilling applications is its thixotropic behavior – the ability to transform between gel and liquid states depending on mechanical stress. When at rest, bentonite drilling mud forms a gel-like structure, but it becomes more fluid when agitated or pumped.
This unique characteristic provides dual benefits: – During circulation, the fluid state allows efficient pumping and movement of cuttings – When circulation stops, the gel state prevents cuttings from settling back to the bottom of the borehole
Swelling and Hydration Mechanism
When bentonite particles come into contact with water, they undergo a remarkable transformation. The bentonite clay drilling mud platelets absorb water molecules between their layers, causing significant expansion. This hydration process creates a colloidal suspension with exceptional properties for drilling applications.
The swelling mechanism involves: 1. Initial water absorption between clay platelets 2.
Separation of platelets as water molecules penetrate
3. Formation of a three
dimensional structure that creates viscosity and gel strength, This process typically requires 12-24 hours for complete hydration, which is why proper
pre-mixing and hydration time is essential for optimal performance.
Filter Cake Formation
Perhaps one of bentonite clay drilling mud ’s most critical functions in drilling is its ability to form a thin,low-permeability filter cake on the borehole wall. As drilling fluid circulates, hydrostatic pressure forces water from the mud into the surrounding formation. The bentonite particles are filtered out at the borehole wall, creating a protective barrier that:
- Prevents excessive fluid loss into the formation
- Stabilizes the borehole wall against collapse
- Seals porous formations to maintain circulation
- Minimizes formation damage
The quality of this filter cake – its thickness, geçirgenlik, and strength – directly
impacts drilling efficiency and well productivity.
Applications and Benefits of Bentonite Clay Drilling Mud
Primary Functions in Drilling Operations
Bentonite drilling mud serves multiple critical functions simultaneously:
- Cuttings Transport: The viscosity of bentonite mud efficiently carries drill cuttings
from the bottom of the borehole to the surface, preventing bit fouling and
maintaining drilling progress.
- Borehole Stabilization: By forming a filter cake on the borehole wall, bentonit
mud prevents cave-ins and maintains the integrity of the drilled hole, particularly
in unconsolidated formations.
- Cooling and Lubrication: The fluid properties of bentonite mud help cool the drill bit during operation and lubricate both the bit and drill string, reducing wear and extending equipment life.
- Pressure Control: The hydrostatic pressure created by the column of drilling mud
helps control formation pressures, preventing unwanted fluid or gas influx into the
borehole.
- Suspension of Cuttings: When circulation stops (such as when adding drill pipe),
bentonite’s gel strength prevents cuttings from settling back to the bottom of the
hole.Industry-Specific Applications
Water Well Drilling
In bentonite clay drilling mud plays a crucial role in maintaining borehole
istikrar, particularly in sandy or unconsolidated formations. The filter cake formed by
bentonite seals the borehole wall, preventing collapse while allowing for the installation
of well casing and screens.
For shallow wells (typically less than 100 ayak), bentonite concentrations of 2-4% by
weight are often sufficient. The mud system helps bring cuttings to the surface while
minimizing fluid loss into the surrounding formation.
Oil and Gas Drilling
The petroleum industry relies heavily on bentonite-based drilling fluids, especially for
upper hole sections. In these applications, bentonite clay drilling mud provides the foundation for more
complex mud systems that may include additional additives for weight control, filtreleme
özellikler, and stability in challenging environments.
API specifications (particularly API 13A) provide strict standards for bentonite quality in
oil and gas applications, ensuring consistent performance across operations.
Horizontal Directional Drilling (Sabit disk)
In HDD applications, bentonite mud serves the critical function of lubricating the drill
string and reducing friction during the pull-back phase. The mud also helps stabilize the
borehole in unconsolidated formations and carries cuttings out of the hole.
The thixotropic properties of bentonite are particularly valuable in HDD, as they allow
the mud to gel when static, preventing collapse during pauses in the drilling process.
Selecting the Right Bentonite for Your Drilling Project
Quality Indicators and Standards
When selecting bentonite for drilling applications, several key quality indicators should
be considered:
- Yield: Measured in barrels of 15 centipoise mud per ton of bentonite, yield
indicates how much usable drilling fluid can be produced from a given quantity of
bentonit. High-yield bentonite (150-200 barrels per ton) is generally preferred for
drilling applications.Viscosity: Measured using a Marsh Funnel, viscosity indicates the flow
characteristics of the hydrated bentonite. Optimal viscosity depends on the specific
drilling application and formation characteristics.
Filtration Control: The ability to form an effective filter cake is measured through
API fluid loss tests, which quantify the volume of filtrate lost under standardized
conditions.
Particle Size Distribution: Finer particle sizes generally produce better suspension
and filtration properties, though extremely fine particles may be difficult to mix
and hydrate properly.
API Specifications: For many drilling applications, bentonite should meet API 13A
özellikler, which establish minimum requirements for various properties
including yield, viskozite, and filtration control.
Comparing Wyoming Bentonite vs. Other Sources
Wyoming bentonite is widely recognized as the gold standard for drilling applications
due to its high sodium content and exceptional swelling capacity. Fakat, other
sources may be suitable depending on availability and specific project requirements:
Characteristic
Wyoming Sodium
Bentonit
Other Sodium
Bentonites
Calcium
Bentonit
Şişme Kapasitesi
15-18 times dry
volume
10-15 times dry
volume
2-3 times dry
volume
Yield (bbl/ton)
150-200
100-150
30-60
Viscosity
Development
Excellent
Good
Poor without
treatment
Filter Cake Quality
Excellent
Good
Fair
Cost
Higher
Moderate
Lower
For critical drilling applications, the superior performance of Wyoming bentonite often
justifies its higher cost through improved efficiency and reduced complications.
- Preparing and Using Bentonite Drilling Mud: Best
Practices
Mixing Techniques for Optimal Performance
Proper mixing is crucial for developing the full potential of bentonite drilling mud.
Follow these steps for optimal results:
Pre-planning: Calculate the required volume of mud and bentonite concentration
based on borehole diameter, depth, and formation characteristics.
Equipment Setup: Use a proper mixing system with high shear capability. A
venturi hopper or high-speed mixer provides better dispersion than simple stirring.
Water Preparation: Begin with clean, fresh water. If water hardness exceeds 100
ppm, consider treating with soda ash (sodium carbonate) at a rate of 0.5-1.0 kg per
1,000 liters of water.
Gradual Addition: Add bentonite slowly through a hopper or venturi system while
maintaining circulation. Adding too quickly will result in clumping and incomplete
hydration.
Continuous Mixing: Maintain circulation for at least 15-20 minutes after adding all
bentonite to ensure thorough dispersion.
Hydration Time: Allow sufficient time (preferably 12-24 saat) for complete
hydration before use. This patience pays dividends in improved performance.
Quality Check: Before use, test the mud properties including viscosity, yoğunluk,
and pH to ensure they meet the requirements for your specific application.
Concentration Guidelines for Different Applications
The optimal concentration of bentonite varies depending on the specific drilling
application and formation characteristics:
Başvuru
Typical Concentration
(% ağırlıkça)
Comments
Water Well Drilling
(Shallow)
2-4%
For stable formations with
minimal fluid loss concerns
4-6%
- Başvuru
Typical Concentration
(% ağırlıkça)
Comments
Water Well Drilling
(Deep)
Higher concentration for
increased borehole stability
Sabit disk (Soft
Formations)
3-5%
Balanced for lubricity and
cuttings transport
Sabit disk (Hard
Formations)
4-6%
Higher concentration for
improved cuttings suspension
Oil & Gas (Surface
Hole)
4-7%
Base for additional treatment as
needed
Geotechnical
Drilling
3-5%
Adjusted based on sampling
requirements
Remember that these are starting points – actual concentrations should be adjusted
based on observed performance and specific project requirements.
Monitoring and Maintaining Mud Properties
Once in use, bentonite drilling mud requires regular monitoring and maintenance to
ensure optimal performance:
Regular Testing: Check viscosity, yoğunluk, and pH at least once per shift or
whenever significant changes in drilling conditions occur.
Viscosity Adjustment: If viscosity becomes too high (making pumping difficult or
preventing cuttings from settling in the mud pit), dilute with water. If too low
(resulting in poor cuttings transport), add more bentonite or viscosity enhancers.
Solids Control: Remove excess drill solids using desanders, desilters, or settling
pits to maintain mud quality and prevent excessive thickness.
pH Maintenance: Keep pH between 8.5-9.5 for optimal bentonite performance.
Adjust with soda ash (to increase) or citric acid (to decrease) as needed.
Fluid Loss Control: If excessive fluid loss occurs, consider adding additional
bentonite or specific fluid loss reducers like CMC (carboxymethylcellulose).
Contamination Management: Be alert for signs of contamination (sudden
changes in viscosity, topaklanma, vesaire.) and treat accordingly based on the
contaminant type.
- Proper maintenance extends the useful life of drilling mud and prevents many common
drilling problems before they occur.
Troubleshooting Common Issues with Bentonite
Sondaj çamuru
Problem: Poor Hole Cleaning and Cuttings Transport
Symptoms: – Excessive torque and drag – Slow drilling rate – Cuttings accumulation in
mud pits – Difficulty circulating after connections
Potential Solutions: 1. Increase mud viscosity by adding more bentonite 2. Increase
circulation rate if equipment allows 3. Implement more frequent wiper trips to clean the
hole 4. Consider adding polymers to enhance carrying capacity 5. Ensure proper mud pit
design to allow adequate settling time
Problem: Excessive Fluid Loss
Symptoms: – Decreasing mud volume in active system – Formation of thick filter cake –
Difficulty maintaining hole stability – Potential for differential sticking
Potential Solutions: 1. Increase bentonite concentration 2. Add specific fluid loss
reducers (CMC, PAC, or starch) 3. Ensure complete hydration of bentonite before use 4.
Check for contamination that may be affecting bentonite performance 5. Consider pre
treating water if hardness is an issue
Problem: Mud Flocculation
Symptoms: – Rapid, unexpected increase in viscosity – Poor filtration control –
Separation of solids from liquid phase – Ineffective hole cleaning
Potential Solutions: 1. Check and adjust pH to 8.5-9.5 2. Treat hardness contamination
with soda ash 3. Dilute system and rebuild with fresh bentonite 4. Add deflocculants if
appropriate for the system 5. Identify and address the source of contamination
Problem: Inadequate Hole Stability
Symptoms: – Hole enlargement beyond bit size – Fill on bottom after trips – Difficulty
running casing – Partial or complete collapse of borehole
Potential Solutions: 1. Increase bentonite concentration for better filter cake formation
- Maintain adequate hydrostatic pressure 3. Minimize time with drill string out of hole 4.Consider adding polymers or other stabilizers 5. Adjust drilling practices to minimize
erosion of borehole wall
Bentonite vs. Alternative Drilling Fluids: A Comparative
Analysis
Bentonite-Based Systems vs. Polymer Systems
Aspect
Bentonite-Based
Systems
Polymer Systems
Initial Cost
Lower
Higher
Environmental Impact
Generally lower, doğal
material
Varies by polymer type
Formation Damage
Potential
Moderate – can be difficult
to remove
Lower – many break down
naturally
Temperature Stability
Excellent up to 300°F
(149°C)
Variable, some degrade at high
temperatures
Filtration Control
Excellent with proper
maintenance
Good to excellent depending
on polymer
Carrying Capacity
Good
Excellent for some polymers
Lubricity
Moderate
Often superior
Ease of Mixing
Requires careful
procedure
Generally simpler
Breakdown for
Development
More difficult
Often easier
When to Choose Bentonite vs. Alternatives
Favor Bentonite When: – Cost is a primary concern – Drilling in stable formations – High
temperatures are expected – Long-term stability is required – Natural materials are
preferred
Consider Alternatives When: – Drilling in highly productive aquifers where
development is critical – Enhanced lubricity is needed (such as long HDD installations) -Rapid breakdown after drilling is required – Specific formation challenges exist that
bentonite alone cannot address – Environmental regulations restrict bentonite use
Many modern drilling operations use hybrid systems that combine the benefits of
bentonite with polymers or other additives to achieve optimal performance for specific
conditions.
Environmental Considerations and Best Practices
Environmental Impact of Bentonite Drilling Mud
While bentonite is a natural material with relatively low environmental toxicity,
responsible use requires consideration of several factors:
- Aquatic Impacts: Bentonite suspension in water bodies can increase turbidity,
potentially affecting aquatic organisms by reducing light penetration and
impacting gill function in fish.
- Soil Effects: Bentonite can alter soil structure and permeability when introduced in
large quantities, potentially affecting vegetation growth.
- Groundwater Considerations: Residual bentonite in aquifers may reduce
permeability and affect well yield if not properly developed after drilling.
- Disposal Challenges: Proper disposal of used drilling mud requires consideration
of local regulations and environmental protection measures.
Sustainable Practices in Bentonite Use
Implementing these practices can minimize environmental impact while maintaining
drilling effectiveness:
- Precise Calculation: Determine the minimum effective concentration needed for
your specific application to avoid excess use.
- Containment Systems: Use proper mud pits with liners or tanks to prevent
unintended release into the environment.
- Recycling and Reuse: Implement solids control equipment to extend mud life and
reduce total volume needed.
- Proper Disposal: Follow local regulations for disposal of used drilling fluids, Hangi
may include dewatering, solidification, or treatment before disposal.5. Spill Prevention: Maintain equipment properly and have spill response plans in
place to quickly address any accidental releases.
- Consider Biodegradable Additives: When appropriate, use biodegradable
polymers and additives in conjunction with bentonite to reduce environmental
persistence.
Advanced Applications and Future Trends
Innovations in Bentonite Technology
The drilling industry continues to evolve, with several innovations enhancing the
performance of bentonite-based drilling fluids:
- Nanoparticle Enhancement: Research shows that adding nanoparticles to
bentonite systems can significantly improve filtration control and thermal stability,
extending applications to more challenging environments.
- Environmentally Enhanced Formulations: New bentonite products incorporate
biodegradable additives that maintain performance while reducing environmental
impact.
- High-Performance Bentonite Blends: Specialized blends combining selected
grades of bentonite with performance enhancers offer superior properties for
specific applications.
- Automated Mixing and Monitoring Systems: Digital technology now enables
precise, automated mixing and real-time monitoring of mud properties, ensuring
consistent quality.
Emerging Applications in Specialized Drilling
Beyond traditional drilling, bentonite is finding new applications in specialized fields:
- Geothermal Drilling: As renewable energy grows, bentonite systems are being
optimized for the unique challenges of high-temperature geothermal drilling.
- Carbon Capture and Storage: Drilling for CO₂ injection wells requires specialized
fluid systems, often based on bentonite, that prevent contamination and ensure
long-term wellbore integrity.
- Microtunneling: Urban infrastructure development increasingly relies on
bentonite slurries for lubrication and support in microtunneling operations.4. Environmental Remediation: Specialized bentonite formulations are being
developed for use in environmental drilling where minimal impact is critical.
Conclusion: Maximizing the Benefits of Bentonite Clay
in Drilling Operations
Bentonite clay remains a cornerstone of effective drilling operations across multiple
industries due to its unique properties and versatility. By understanding the science
behind its performance and implementing best practices in selection, preparation, Ve
maintenance, drilling professionals can maximize efficiency while minimizing
complications.
The key takeaways for successful use of bentonite drilling mud include:
- Quality Matters: Invest in high-quality bentonite that meets industry specifications for your application.
- Preparation is Critical: Take the time to properly mix and hydrate bentonite before use.
- Monitoring Ensures Success: Regularly check and maintain mud properties throughout the drilling process.
- Adaptability is Essential: Be prepared to adjust mud properties as drilling
conditions change.
- Environmental Responsibility: Implement sustainable practices in the use and
disposal of bentonite drilling fluids.
Whether you’re drilling water wells, oil and gas wells, or horizontal directional drilling
projects, proper use of bentonite clay drilling mud provides the foundation for
successful operations. By applying the principles and practices outlined in this guide,
you can achieve optimal drilling performance while minimizing complications and
çevresel Etki.
Need Expert Assistance with Your Drilling Project?
Our team of drilling specialists is ready to help you select the right bentonite products
and develop optimal mud programs for your specific application. With decades of
combined experience across all drilling disciplines, we provide:
- Customized mud program design• On-site technical support
- Troubleshooting assistance
- Product selection guidance
- Training for your personnel
Contact us today to discuss how we can help optimize your drilling operations and
maximize efficiency.
[Contact Form/Information]
Frequently Asked Questions
Q: How much bentonite should I add to my drilling fluid?
A: The optimal concentration depends on your specific application and formation
characteristics. For water well drilling, concentrations typically range from 2-6% by
weight (15-50 pounds per 100 gallons of water). For more precise recommendations
based on your specific project, contact our technical team.
Q: How long does bentonite drilling mud need to hydrate before use?
A: While some benefits are seen after just 30-60 minutes of mixing, optimal performance
requires 12-24 hours of hydration time. This patience allows the bentonite platelets to
fully separate and develop their colloidal structure.
Q: Can I reuse bentonite drilling mud?
A: Evet, with proper maintenance. Remove drill solids using settling pits or mechanical
separation equipment, adjust properties as needed, and the mud can be reused for
extended periods. This practice reduces both costs and environmental impact.
Q: Is bentonite environmentally safe?
A: Bentonite is a natural clay mineral with relatively low toxicity. Fakat, it should be properly contained during drilling and disposed of according to local regulations to prevent environmental impacts such as increased turbidity in water bodies or soil structure changes.
Q: What’s the difference between drilling-grade bentonite and pond sealing
bentonit?
A: While both are sodium bentonite, drilling-grade bentonite is processed to specific particle size distributions and meets performance standards for viscosity and filtration control. Pond sealing bentonite is optimized for swelling and creating impermeablebarriers but may not provide the rheological properties needed for effective drilling fluids.
Q: How do I know if my bentonite mud is too thick or too thin?
A: A Marsh Funnel test provides a simple field measurement of viscosity. For most water well applications, a Marsh Funnel viscosity of 35-45 seconds is appropriate. Too thick (>60 seconds) may cause pumping difficulties, while too thin (<30 seconds) may not adequately clean the hole or maintain stability.